Construction companies of all sizes need cost-effective solutions for managing spatial details when working on projects in the healthcare space. Technologies to access reality capture are now affordable and adaptable to the needs of all types of construction-related businesses, making it possible for varied contractors and owners to share valuable data. Healthcare site reality capture that seamlessly integrates with BIM and project management software can support builders' work in creating spaces that conform to the needs of healthcare professionals.
Healthcare construction spending is increasing in the United States, with a 40% increase at the beginning of 2024 from 2020. Worldwide, the healthcare construction pipeline is valued at $625 billion. Innovation in hospital construction methods will help builders meet the challenges of today’s construction market realities, including time and budget constraints, increasingly complex medical infrastructure needs, and the multiple stakeholders involved in creating spaces for public and private healthcare organizations.
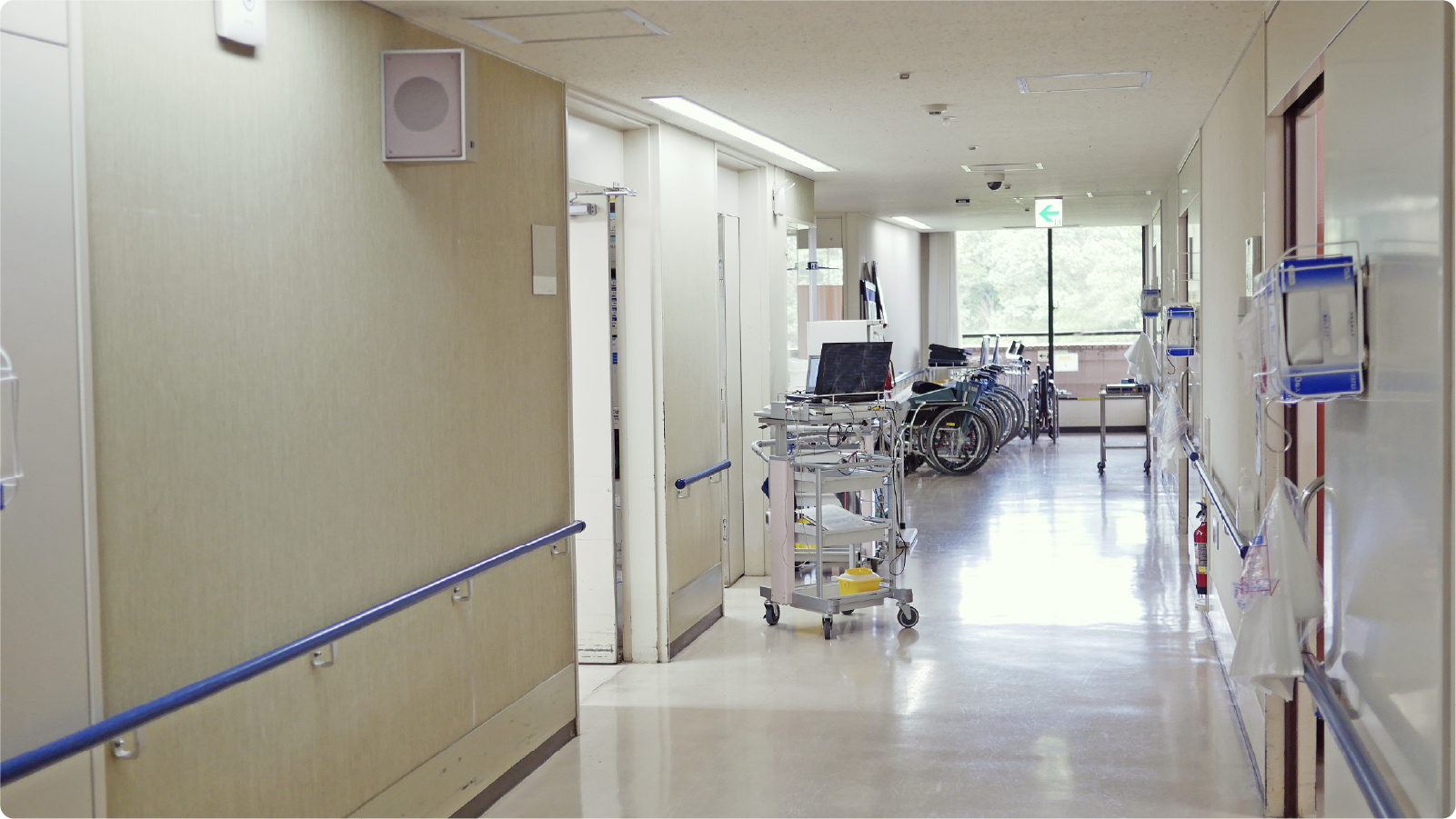
Digital Twins in Healthcare Construction
Just as digital patient twins help medical professionals better understand and treat conditions and diseases, digital twins used in construction help builders achieve the precision and control to manage construction projects for healthcare facilities of all types accurately. Site replicas that can marry 2D plans and 3D documentation with 3D imaging help not just in clash detection and project management but can also assist everyone, from owners and designers to the workers on site, in grasping the details of the building under construction or renovation.
Builders who specialize in healthcare and hospital construction understand the complexities of the work required to meet the exacting and expensive delivery of advanced medical treatments. But with the growing need for renovation, new construction, and retrofitting for healthcare spaces of all types, even builders of less technologically complex projects will see the need to work with the more stringent requirements for spaces such as doctors’ offices and healthcare clinics in their jurisdictions.
Creating future-ready spaces that can adapt to the changing nature of healthcare and fluctuations in use due to pandemic and natural disaster-related health crises is a challenge. Using hospital site reality capture during the building process allows contractors to be more efficient and precise.
![Optimize rebar inspections with CupixWorks' powerful annotation feature. Streamline your process by effortlessly reviewing and submitting checklists using the annotation tool, consolidating and archiving your inspection reports in one convenient location.]()
Top Healthcare Construction Challenges:
Adopting reality capture technology can help contractors and facility owners better manage the challenges of healthcare and hospital construction. Here are some of the issues inherent in constructing medical spaces that digital twin technology can help to address.
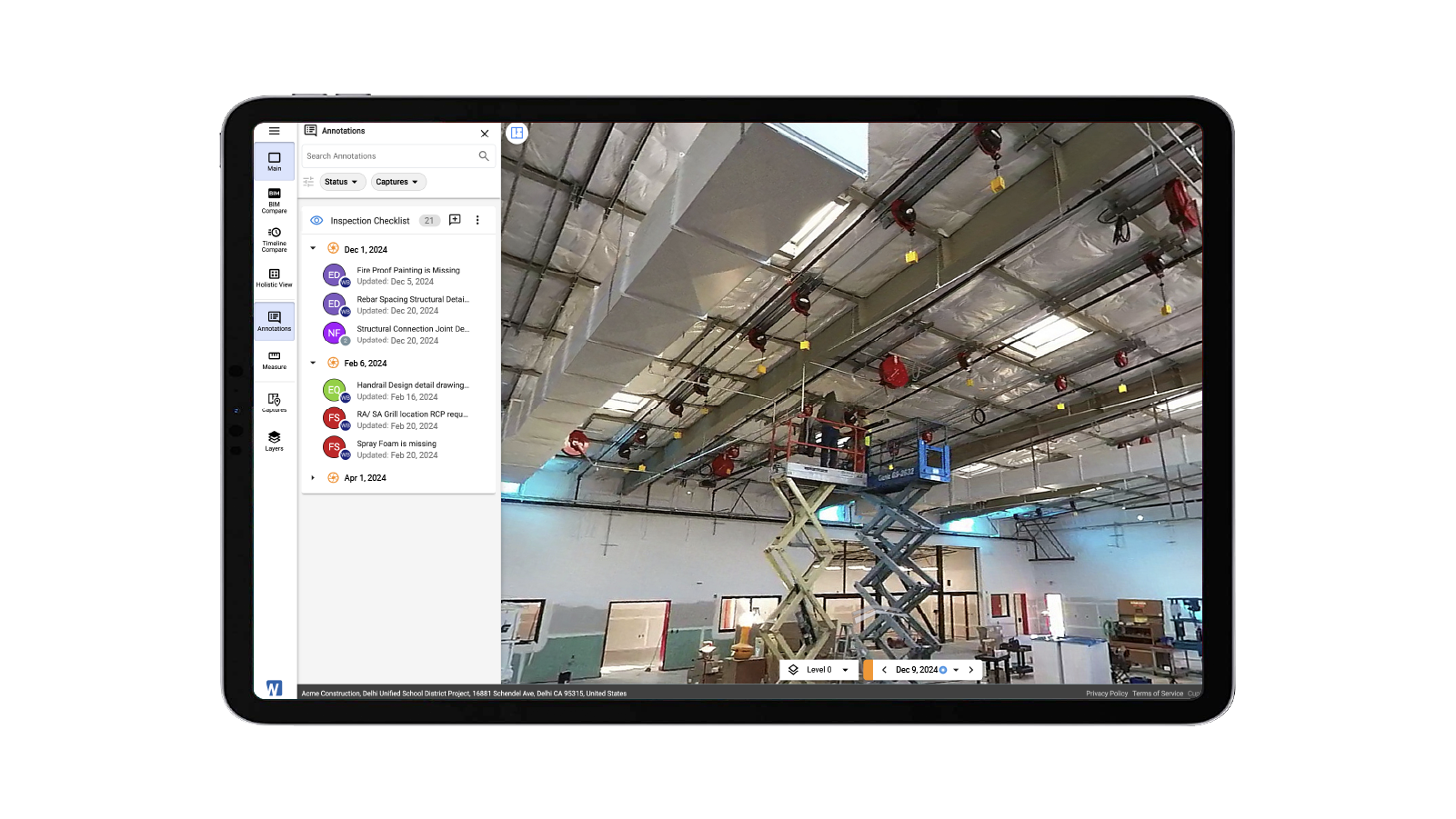
1. Keeping Multiple Stakeholders Involved and Informed
Construction projects always involve many stakeholders, including the owner, general contractor, and trade partners. However, when building medical facilities, the owners have specialized medical personnel alongside the business representatives to ensure that the project will function as needed for healthcare procedures, infection control, healthcare teams, and patients. In addition, regulators have strict requirements builders need to achieve to remain compliant during construction and for the finished product.
Communication during preconstruction and on-site work needs to be clear and specific to the issue being discussed. Identifying the precise location of a problem and visualizing it is vital to having a productive discussion and arriving at solutions that meet all requirements. Geotagging areas to discuss allows all stakeholders to understand the verbal and spatial information and can reduce the probability of miscommunication.
Not all stakeholders will fully understand the construction process or the technical realities of the build, so tailoring presentations to meet viewers’ needs for information will assist builders in positive communication with varied audiences. Medical professionals like doctors and nurses are deeply invested in their workspaces, which accommodate medical interactions and foster patient comfort, but they may not fully appreciate all the specialty work needed to get there. The ability to show virtual tours and 3D visualizations and compare them to current spaces can help healthcare practitioners understand the construction project’s progress.
Conversely, trade partners and medical equipment installation experts are intensely focused on the details that impact their highly technical work. The ability to access multiple visual perspectives of as-built conditions alongside BIM with exact placements dramatically enhances the communication between the professionals tasked with ensuring that every detail is compliant and functional.
2. Realizing Complex Designs with Precision
Building healthcare spaces requires precision to accommodate complicated infrastructure and equipment. Dental offices, radiology practices, and doctor’s offices may not have the level and complexity of a hospital site reality capture, yet they require expensive equipment placement and MEP (mechanical, electrical, and plumbing) to perform specific functions. Healthcare space design has less room for error as trades cycle through a work site. Any slight deviation in measurements or placement of elements can require expensive rework down the line.
Although the details of each design will vary, accuracy is a foundational requirement in healthcare builds. Digital twins in healthcare construction can already be used to quickly and accurately note clashes or inconsistencies between design and reality on the hospital site. The ease of using a 360° camera to walk the site before work begins and then frequently during construction can assist all trades and the GC in managing any tiny errors before they become major headaches. Integrating all of the geospatial information available for a site and sharing it in a cloud-based collaborative platform like Cupix can assist design teams, project management, and quality assurance to maintain adherence to plans and resolve problems early in the cycle to reduce costs associated with delayed rework.
3. Tight Budgets and Schedules
The large scale of many healthcare construction projects means budgets are similarly large, and funding is often complex and controlled by many outside entities. Cost overruns are common and funding issues can cause work stoppages, impacting schedules. Many hospital construction projects occur near or within existing hospitals, meaning crews have limited hours in which to work, which can slow the process and limit flexibility to catch up when inevitable glitches impact scheduling. Supply chain issues have also caused delays for construction projects, giving project managers additional scheduling complexity.
Construction digital twin healthcare tools can save time during construction by reducing the number of site visits required to detect and resolve clashes, supporting effective meetings to discuss change orders, and allowing project management personnel to detect issues between the as-built and BIM and resolve any problems that arise on site more quickly. Progress tracking solutions like SiteInsights from Cupix add additional transparency to the status of all of the trades participating. All team and inter-organization communication is more efficient when all stakeholders can access detailed reality capture data to drive their decision-making.
Some projects now utilize the collaborative contracting model, which shows exceptional promise for large capital projects such as healthcare construction. For hospital and health system projects, this mode of contracting has shown a 10-20% improvement in cost performance and a 10-34% improvement in schedule performance over traditional methods. As the name suggests, collaborative contracting requires entities to work smoothly together, and accurate, accessible healthcare site reality capture can help teams stay on the same page.
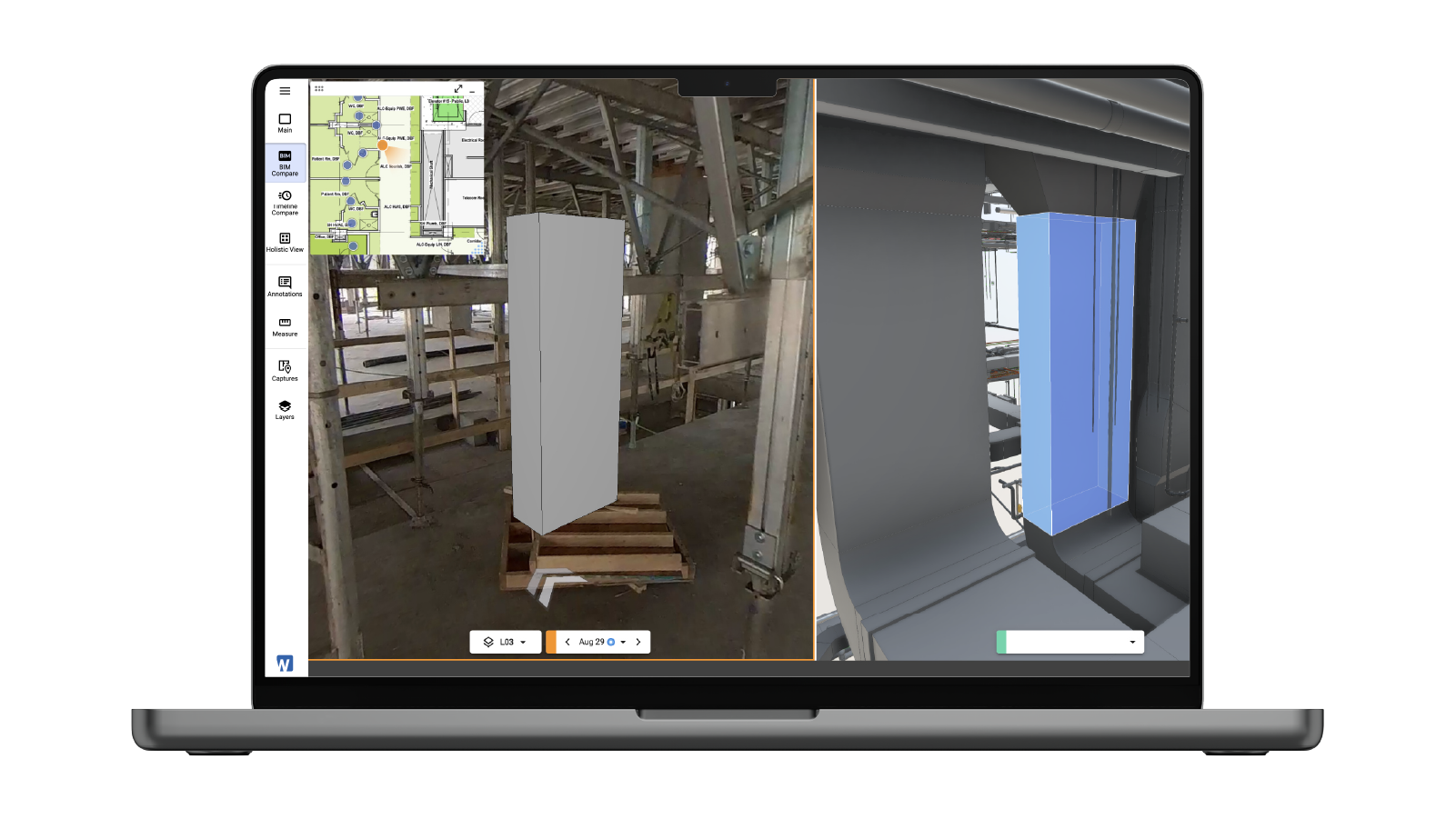
4. Creating Adaptable Spaces
Healthcare is a fast-changing field, with advances in technology, changes in ownership of facilities, and shifting patient needs. Spaces for healthcare change often to accommodate different uses, such as when hospitals change room uses from a general patient ward to an intensive care unit. Also, the expansion of spaces or the need for renovations and upgrades is much more frequent in healthcare spaces. Facilities managers need accurate as-built information to manage the day-to-day upkeep of healthcare spaces and arrange for repairs to equipment or structures. Healthcare spaces also often require frequent technological upgrades to safety systems, such as air quality controls, temperature and humidity monitoring, and security systems.
Healthcare reality capture data allows owners and future contractors to access the visuals of hidden utilities and structural elements easily. Integrated spatial data captured during construction gives as-built information to help plan renovations to HVAC or MEP systems, building structure renovations, and expansions. Facilities managers with access to reality capture information can quickly and efficiently diagnose and locate a functional problem in their systems for repair crews. When rooms are converted to different uses, the location of medical gas lines, HVAC, electrical, and plumbing can be easily located to adapt to the needs of the new use of the space. Exact spatial data greatly aids speedy space usage alterations required in urgent situations in health care.
5. Meeting Regulations and Guidelines for Safety and Quality
Healthcare construction projects are subject to more stringent standards and regulatory agency inspections than other construction projects. Each jurisdiction has regulations for healthcare construction. In addition, The Joint Commission, the Facility Guidelines Institute, and the American Institute of Architects all issue guidelines for healthcare construction. Not only does the finished building need to conform to strict safety codes, but the work performed, especially when patients are present in nearby areas, needs to be carefully monitored. Infection control in healthcare construction is a difficult task, as the materials from renovation, demolition, or new installation can introduce pathogens that patients may be susceptible to into air ducts or spaces. Every step of the construction process needs to be carefully managed to avoid contamination.
Precise spatial data from reality capture can assist in adhering to healthcare construction guidelines and regulations. Project managers can better document and plan healthcare construction with accurate digital twins of the space, limiting the time on site for planning purposes and more carefully scheduling the work. Inspectors can view different stages of the construction to ensure compliance with regulations for specific elements of the build. Quick and frequent site walks with a 360° camera allow off-site managers to assess and monitor the status of protective barriers required to comply with stringent health and safety requirements for healthcare space construction.
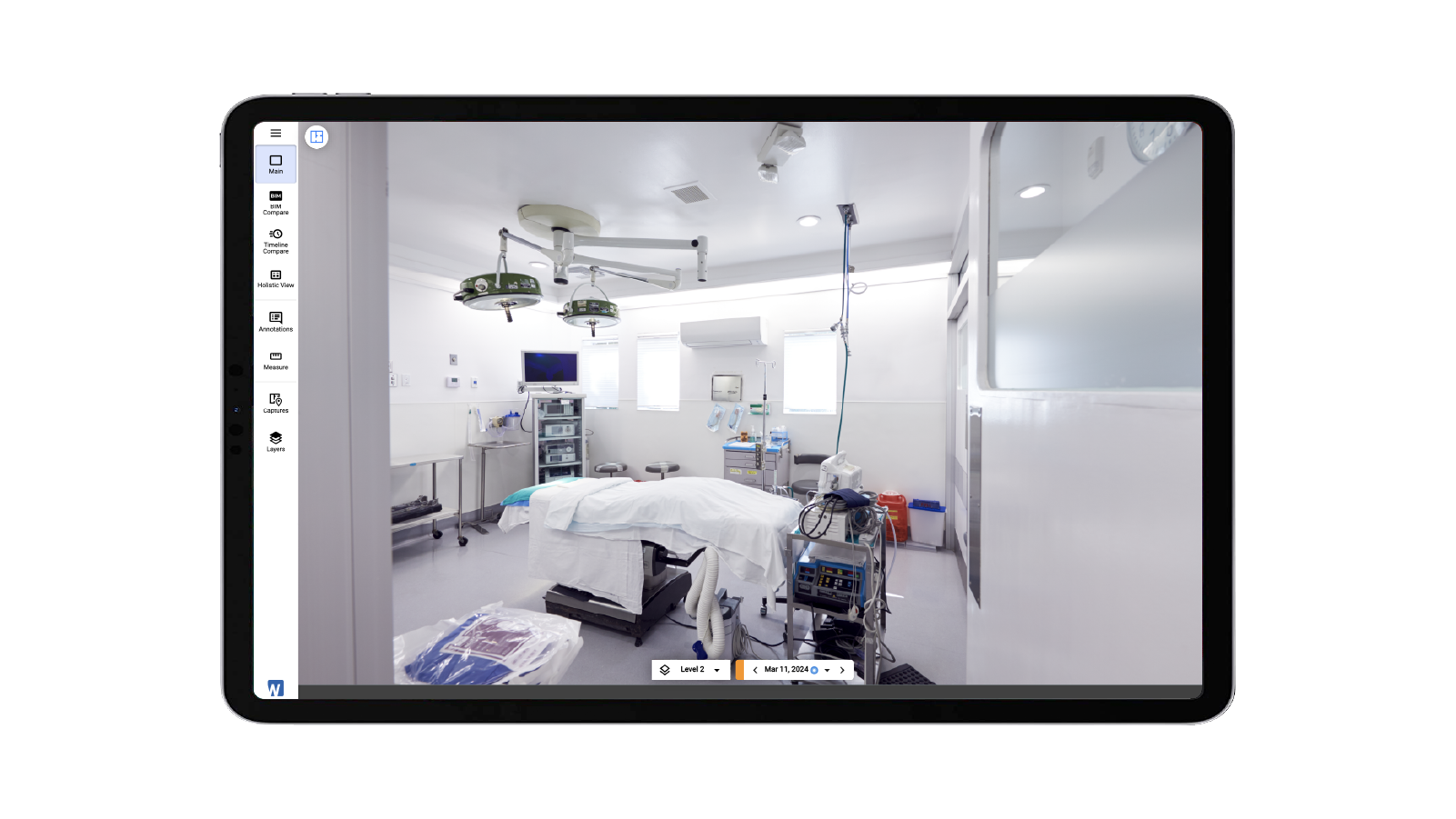
Conclusion
Construction digital twins in healthcare can help owners and builders meet the challenges of constructing hospitals, long-term care facilities, medical offices, and clinics. 3D Reality capture has become a more accessible and affordable option for various stakeholders in the healthcare construction industry to manage their parts of each project with precise spatial data. With solutions like Cupix, integrating digital twins into healthcare construction workflows is simpler than ever, and the gains in productivity, accuracy, and error reduction can make the payoff for adding reality capture a huge win for builders and owners alike.